一.Electroplating production line use
Used for copper plating on customer's products
二.Electroplating production line conditions
1. Power supply: 380V, 50HZ, three-phase four-wire
2. Production line occupies: length 26m* width 8m* height 6m
3. City water: 5T / H, water pressure 2.0 ~ 3.0kgf / cm3
三.Electroplating production line overview
1.XHL-29BL4000 gantry semi-automatic stainless steel production line is a special electroplating equipment designed according to the plating process provided by customers;
2. According to the workflow and work efficiency of the production line, the manual production line is equipped with 3 gantry trains. Manual gantry driving has vertical lifting, lowering and left and right high speed walking functions;
3. The basic operation method is as follows: firstly, the workpiece is manually sent to the predetermined loading position, the working power is turned on, and then the work instruction is started, and the gantry driving starts working. The gantry driving is driven to the loading position under the control of the manual program, the workpiece on the loading level is lifted, then moved to the first working process slot, the workpiece is placed vertically, and so on, and the worker is raised when the material is lowered. Go, the arm will drop the processed workpiece to the blanking position, thus completing the entire production process;
4. Characteristic description: The equipment is beautiful in appearance, compact in structure and reliable in performance;
四. Electroplating production line detailed technical specifications
1. Rack:
The overall structure is a medium-rail type frame, which needs to be pre-buried. In order to prevent the liquid droplets from falling onto the ground during the production process, all the tanks have a cover plate.
A. Rail: 100*100*4mmA3 rectangular square tube; (When installing, ensure the rail level is &cjiamn;3mm, and the two rails are balanced by &cjiamn;2mm to ensure no obvious jitter during driving)
B. Main column: 100*100*4mmA3 rectangular square tube, spray acid and alkali resistant paint
C, wire trough tube support frame is 50*50*2.5mmA3 rectangular square tube, spray acid and alkali resistant paint; driving flat wire chute, induction switch positioning groove adopts 2mm thick galvanized bending parts, spray acid and alkali paint
2. Longmen driving: 3 sets
A, technical parameters
Lifting stroke: 1600mm
Lifting speed: 0-16m/min (frequency converter speed regulation)
Lifting weight: 200kg
Lift motor: 2.2kw high imitation Italian brake motor
Translation speed: 0-10m/min (frequency converter speed regulation)
Translation motor: 1.5kw high imitation Italian brake motor
B, production materials and functions
Driving frame: using 5mmA3 board, spraying acid-proof paint; driving lifting, shifting and driving, driving start, stop stability, and ensuring the running speed and positioning accuracy of the driving; two workshops with limited collision protection to prevent driving failure and derailment Collision; fall with anti-sling reversal protection (anti-hook stuck, always falling anti-crane belt reverse)
Driving casters: using polyurethane plastic bag wheel, running smoothly and with sufficient strength and low noise; guide wheel: using polymer PE wheel, durable wear;
Driving translation drive shaft, lifting drive shaft: chrome enamel rod, both rigid and flexible; lifting: nylon sling; lifting rail: 60*60*3mm SUS304 stainless steel rectangular square tube;
3. Electrical control section
Electric control cabinet: It is made of 1.5mm thick SS41 board, and the surface is sprayed; the internal wiring of the control cabinet is regular, the line number is clear and accurate, the weak part is shielded and isolated from the strong electric cable; the independent power supply is used, and all components on the operation panel are clear. Clear label.
Inverter: Adopting Mitsubishi products, the performance is stable and reliable
Inductive switch: using Delixi products, sensitive and accurate positioning
AC contactor: using Delixi products, durable
4. Tank
A. The washing tank is made of 12mm domestic PPA board. The welding torch is used in the tank to ensure that there is no leakage in the plating tank. The plating tank adopts 15mm domestic PP board, and the welding torch is welded in the tank to ensure no leakage of the plating tank. ;
B. The tank body is strengthened: 100*50*2.5mmSS41 rectangular square tube is used to ensure the plating tank has sufficient strength, and the flat-through outer seal 4mmPP board is protected against corrosion;
C. The overflow of the washing tank is a diagonal overflow, and the overflow bucket is placed outside the tank;
D. A liquid shielding baffle is arranged between the tank bodies to prevent the tank droplets from entering the gap between the tank bodies.
Five. Water supply and drainage pipeline
1. The pipelines shall be arranged according to the pipeline construction specifications. The inlet and outlet pipelines shall be arranged on the side of the operation surface. The design of the pipelines shall be convenient for operation and maintenance. The pipelines shall be arranged neatly and beautifully, without bubbles, dripping, dripping or leaking. Flexible valve operation;
2. All pipeline installation height levels are uniform, and each main pipe is provided with a total control valve as emergency control, and the overall control operation is flexible;
3. The main pipeline such as water supply is placed below the operating platform above the ground. The pipe is made of high-strength and corrosion-resistant UPVC pipe, which is arranged reasonably, does not affect the production and maintenance access, and is easy to operate and maintain;
4. Each tank is provided with independent tap water or pure water supply pipeline according to the process requirements. The inlet water pipeline is directly inserted into the bottom of the tank along the tank wall, and is arranged diagonally opposite to the overflow port. The cleaning water flow is long and the utilization rate is high;
5. The wastewater is divided into acid-base wastewater according to different properties, and the chromium-containing wastewater is discharged into the wastewater treatment station to facilitate the classification and treatment of wastewater;
6. All pipelines are designed to avoid siphoning caused by negative pressure;
7. Tap water and pure water are installed with spare valves and hose joints at both ends of the production line and at the side of the function slot;
8. Water supply: municipal water main 1.5′′ UPVC pipe (reserved with water return switch interface); pure water main 1.5′′ UPVC pipe;
9. Drainage: 3′′ UPVC pipe for integrated wastewater; 2.5′′ UPVC pipe for cyanide wastewater; 2′′ UPVC pipe for acid copper wastewater; 2.5′′ UPVC pipe for alkaline wastewater
Solution circulation and filtration system
1. The material and flow rate of the filter or circulating pump are prepared according to the process requirements to ensure that the pressure requirements of the filter are met; the inlet and outlet of the solution can ensure the convection of the whole tank solution as much as possible, and there is no cycle dead angle to ensure complete solution treatment;
2. According to the nature of the solution and the operating temperature conditions, select different power, lift magnetic pump and filter to ensure the solution circulation, good filtration effect; circulation pump, filter corrosion resistance, with leakage prevention, phase loss, overcurrent With the protection and alarm functions, the filter can easily clean or replace the filter;
7. Bath heating and cooling system
1. The production line is cooled by direct cooling;
2. The heating of the production line is heated by a heating rod;
VIII. DC power system
1. Conductive cable, conductive pole, and conductive copper row have sufficient cross-sectional area;
2. The copper bar should be as close as possible to the connection point, and the connection point should be flattened and tightened with stainless steel screws after being polished or conductive paste;
3. In order to ensure uniform distribution of cathode and anode currents in the tank and no short circuit, all the anode and cathode blocks are provided with insulating blocks (insulation resistance ≥1MΩ) to prevent leakage; each plating tank is independently supplied with power, respectively, and a rectifier is provided;
9. Electroplating production line physical map
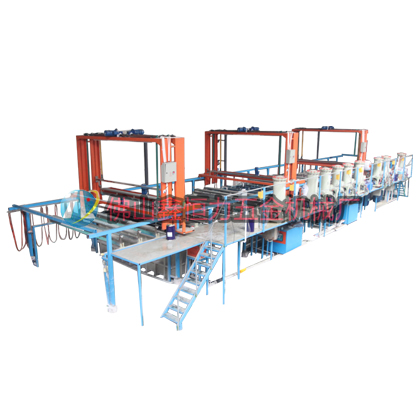