Application of etching die:
Etching cutters are mainly used in electronic materials, printing and packaging, plastic packaging, leather, toys, automobiles, decoration, rubber products, EVA, and various foams, precision electronic gaskets, Mylar sheets, nameplates, flexible circuit boards, etc.
Etching die making process:
A: Order: The salesman is responsible for taking orders and communicating with the customer the production requirements, quotation, and delivery time. After the customer confirms, the mold making sheet is opened, and the layout is started. Finally, the drawings are made into a corrosion-resistant film and the work order is handed over to the Corrosion Department.
Second, chemical corrosion: the etching department receives the film and the work order, confirms the thickness of the plate, and after the material type of the knife is high, the film is printed and exposed. Finally, after development, the mold prototype is revealed. If the exposure is not done properly, the pattern must be repaired before it can enter the corrosion equipment for corrosion. After the requirements are met, the film can be removed and the next department can be sent.
3. CNC engraving: The engraving department receives the protective film cutter after the rough machining. After the visual inspection is confirmed, the machine is placed for processing. Due to the difference in the size and difficulty of the die line, the production time is different. Generally, the protective film die is 1-4 hours, and the special time is 8 hours or even 24 hours to complete the CNC machining. After the completion, the squad leader checks. It is initially determined that there is no problem before it can be sent to QC.
Fourth, QC: QC is responsible for testing the size of the etching die, etching the die cutter blade and so on. It is also responsible for making the inspection report and then sending it to the heat treatment.
V. Mirror surface treatment: This treatment can remove the micro-grain on the side of the etched knife die to achieve the mirror effect, which can effectively solve the problem of burr dust when punching and cutting the product, so that the edge of the product is smooth and smooth. Suitable for punching products with higher requirements.
How to choose the right chemical corrosion machine in the process of etching die?
The traditional chemical etching machine is divided into a splash etching machine and a horizontal etching machine. However, in actual production process, the etching precision is often difficult to control due to various reasons, and it is easy to produce corrosion detection; Foshan Xinhengli Hardware Machinery Factory Through market feedback and years of experience in etching equipment manufacturing, we developed a reverse-spray rotary etch machine (the size of the turntable can be customized), the workpiece is clamped on the turntable, and the independent swing sprayer is sprayed from the bottom to the high pressure. The turntable also rotates, thus avoiding the residue of the etching liquid on the surface of the workpiece and improving the etching precision. At the same time, the rotary etch machine comes standard: 4KW vertical acid-resistant pump, full-pressure filter, titanium alloy heating tube, titanium alloy water-cooled tube, temperature display automatic heating system and so on. I plant equipment can be customized, welcome new and old customers to visit the factory and negotiate business, Xin Hengli Hardware Machinery Factory all colleagues look forward to working with you hand in hand, mutual benefit and win-win!
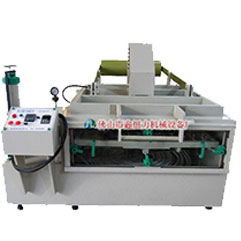
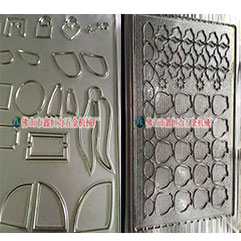